Improving your packaging process involves eliminating waste and increasing efficiency. It starts with ensuring the tasks are simple. Any complex tasks can cause errors, time wastage, and added costs. Regardless of the type of packaging you have, efficiency should be your number one priority. While this won’t happen overnight, it is something that you can do gradually over time. These 5 ways to improve your packaging process will help you make the most of every moment and improve your product’s overall quality.
Automated systems reduce labor costs.
When your company uses automated systems in your packaging process, it can save your company money in several ways. While most packaging processes still require labor, automating your process can increase efficiency. By automating essential tasks, you’ll be able to produce more products at a lower cost per case and maximize your bottom line. The following are just a few ways that automated systems can improve your packaging.
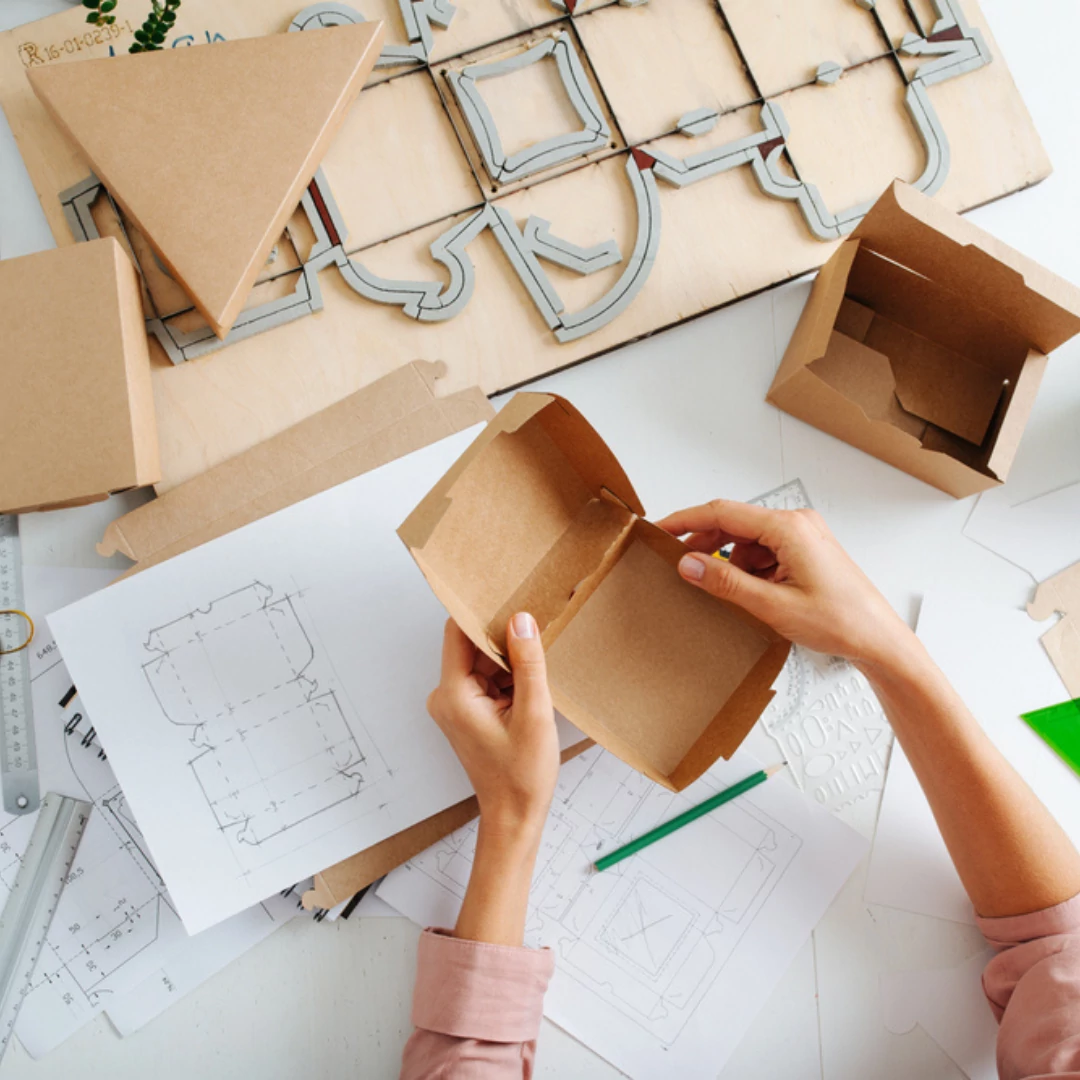
Automated systems reduce human error. Automating your packaging process can help reduce employee turnover, slow production and delay the delivery of finished goods. Additionally, automatic machinery won’t call in sick or leave for another job, allowing you to reassign the labor you currently have. In many cases, automated systems can save your business up to $35,000 per year! These benefits make mechanical systems the more brilliant choice for your packaging process.
Foam-in-place reduces product shift.
One of Unipaq’s most versatile packaging solutions, the Foam-In-Place Cushioning System molds foam around any product, regardless of size or shape. The foam-in-place system reduces product shift because it takes up a small fraction of space. Additionally, because it is a lightweight, environmentally-friendly solution, it is easy to recycle. Foam-in-place reduces product shift by 80% and has no adverse effects on the environment.
Foam-in-place packaging forms a protective mold around the contents of a package, reducing product shift and the risk of writing-off damage expenses. The technology makes sure that the product arrives in the same condition as when it was shipped, increasing consumer confidence and giving businesses an excellent first impression. However, foam-in-place is not suitable for every product. For example, 10% of all packages are damaged in transit, with 5% of the damage resulting in product shift and loss.
Printing the label directly onto the package reduces waste.
By printing the label directly on the package, you will save on paper, ribbons, and other materials that would otherwise be discarded. This technology reduces waste by removing label backing and ribbons and reduces waste in packaging departments. It also requires no hazardous chemicals. Changing printing methods can also help to reduce waste. If you’re currently using traditional methods, consider digital printing techniques instead.
On-Demand production of right-sized packaging
On-Demand production of right-size packaging is a solution that brings together precision right-sizing technology with a complete array of accessories and services. It allows companies to replace pre-made box inventories and wasteful void filler with customized packaging that saves resources, is dimensionally superior, and improves your packaging process. Packsize is a pioneer in this field, providing a full range of solutions for various industries.
By using the right-sized packaging, businesses can save up to 40% on material, cut labor by up to 60%, and reduce void fill by up to 60%. This results in a 25-ton CO2 reduction globally. Right-sized boxes are ideal for e-commerce companies because they reduce the risk of shifting and damage. It also reduces the number of filler products and packages in your supply chain.
Virtual-reality training helps new hires retain information.
Companies realize the benefits of VR for learning. Virtual-reality training helps new hires retain information during the packaging process. Earlier, training workers in a store would require travel and group instruction days. In contrast, VR enables mental repetitions in a safe environment, making it more realistic. Verizon wanted to teach its employees how to respond to an armed robbery in one case. The company stressed the importance of worker safety in its VR training.
In addition to the benefits of VR training, the immersive nature of the software allows employees to learn faster than in a traditional classroom environment. The study by PwC found that employees trained in VR learned more than their counterparts who learned through e-learning. For example, a course that would take an hour to complete in a classroom could be completed in 20 minutes through VR. Immersive VR can help new hires focus better because it reduces distractions. They can ask repetitive questions without losing patience.